Encore une nouvelle turbine d'aspi
+5
dh42
max91800
meles
sangten
napo7
9 participants
Page 2 sur 2
Page 2 sur 2 • 1, 2
Re: Encore une nouvelle turbine d'aspi
Hier soir, petit (court) séjour à l'atelier.
Il faisait déjà -3° dehors, l'atelier n'est pas isolé, il devait pas faire beaucoup plus chaud dedans !
J'ai donc démonté mon ancien "aspirateur".
En fait, la turbine était encore en bon état. Je l'ai fait tourner, elle tourne par contre comme une patate !!
Hors de question de garder ça, je vais donc en faire une nouvelle.
Pour mon prochain test, j'ai donc prévu de la faire en PVC.
J'ai une grande plaque, d'environ 1m par 2m, en 10mm d'épais, cela ressemble plutot à du FOREX: l'âme n'est pas "lisse" comme la surface, mais granuleuse (fin quand meme). Elle semble cependant assez dure, et ne s'enfonce pas sous l'ongle... Ca n'est donc pas une "mousse molle".
Le temps, ou plutot l'experimentation, dira si ca convient... Je me suis un peu documenté sur ce matériaux, il s'assemble comme du PVC classique: usinage aux outils à bois à basse vitesse, collage à la colle PVC, "soudage" (que je ne tenterai pas...)
Allons y, alors, avec la découpe du disque de base de la turbine.
Après avoir coupé grossièrement un carré d'environ 50cm de côté à la scie sauteuse, je traçe ma turbine sur le PVC.
Tout au compas : Je marque le centre, puis un premier diamètre, et le cercle.
J'ai décidé de mettre 8 ailettes à la turbine. Il faut donc diviser ce cercle en 8. En 6, c'aurait été facile, il suffit de tracer une rosace
En 8, ca n'est pas beaucoup plus compliqué, il suffit de se souvenir de ses cours de trigo ! Est ce que mon prof de maths aurait cru qu'un jour j'allais fabriquer une turbine dans mon atelier !
Après avoir tracé le cercle et un diamètre, on fait donc une perpendiculaire à ce diamètre passant en sous centre. Au compas, c'est rapide et précis.
Puis, on trace les 4 bissectrices des 4 quadrants représentés par ces deux droites. Encore facile et rapide au compas !
Voila, mon cercle est divisé en 8, il faut ensuite tracer la position des 8 ailettes.
J'ai choisi de les orienter vers l'arrière (il semble que la turbine garde des performances plus "linéaires" avec cette configuration).
Je trace donc un second cercle , assez petit, au centre du premier, et je décale le tracé de chaque ailette.
Au final, après quelques minutes, on est prêt à défoncer tout ça :
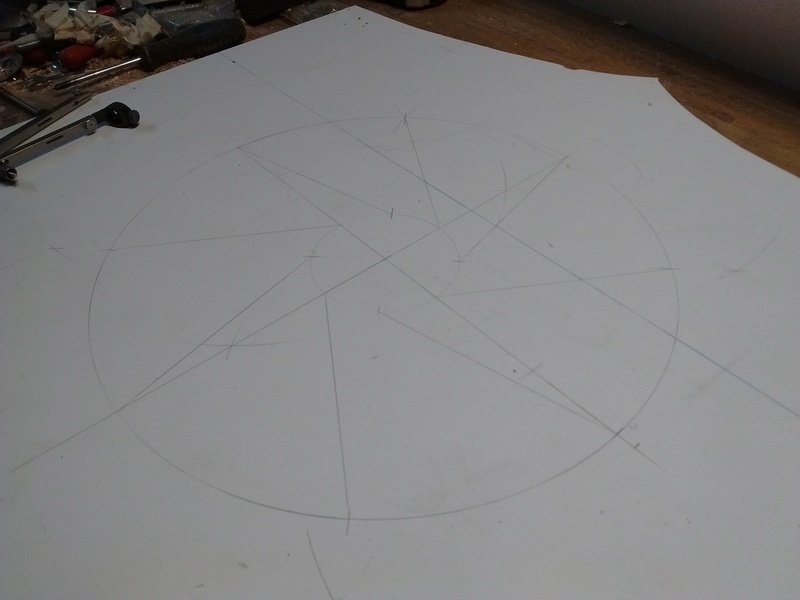
Un petit trou diamètre 5mm au centre, et la défonçeuse prend place avec son compas :
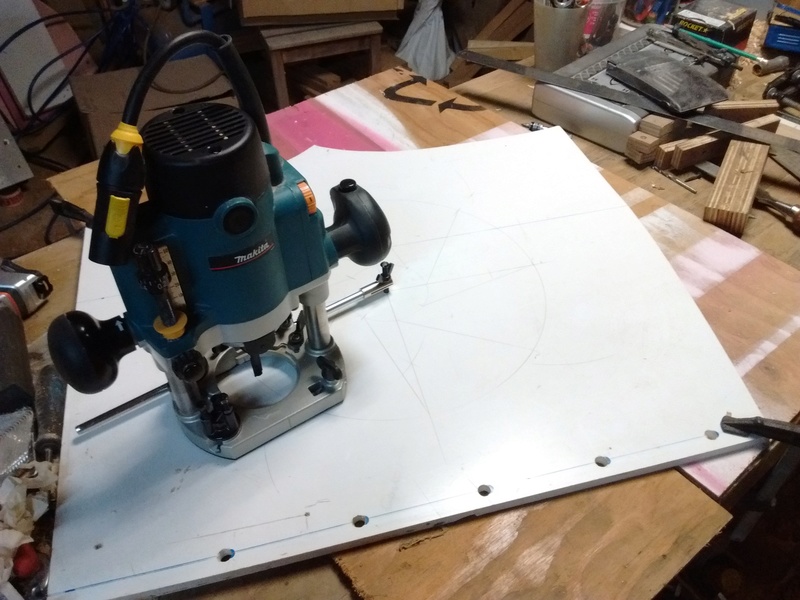
Première passe légère, réglage au plus lent : le matériau se comporte agréablement: Ça fait de petits copeaux, qui ne collent pas.
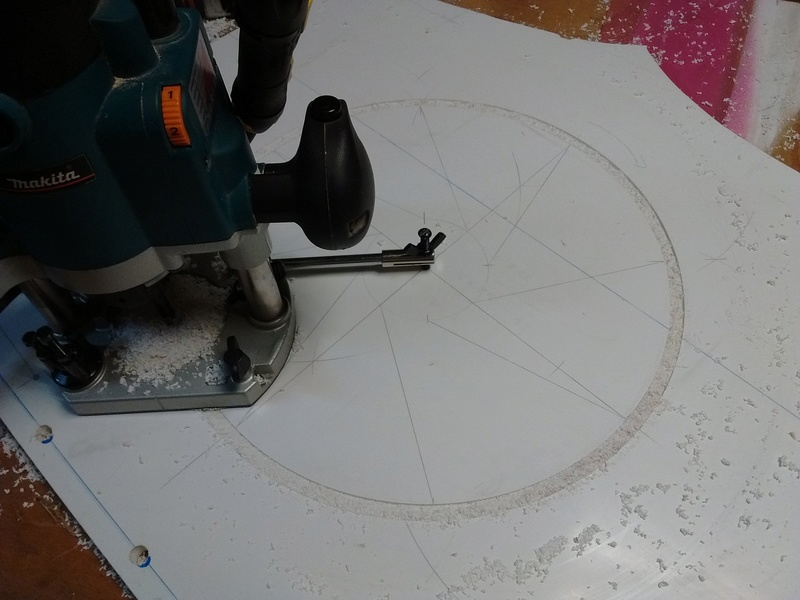
Et voila, le disque est découpé.
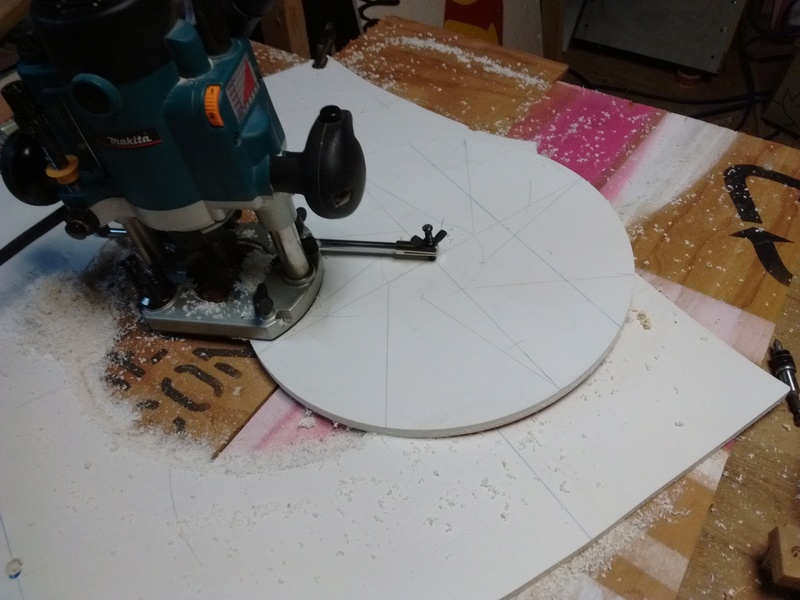
Enfin, je trace une parralèle à 5cm (largeur entre l'axe de la fraise et le coté de la semelle de la défonceuse) de chaque future ailette et je défonce celles-ci.
C'est assez rapide, j'aurais pu me fabriquer un guide, mais il n'y en a que 8 à faire, ca se fait rapidement !

J'ai oublié de prendre une photo une fois terminé ! Oups !
L'établi est tout blanc... J'aurais pu chanter à tue-tête "Il a neigé dans l'atelier..." sur un air bien connu
Enfin, après avoir terminé ces coupes, je me rend compte que j'avais monté une fraise de 8mm sur la défonceuse, et les ailettes feront...10mm d'épais !
Je vais donc pouvoir élargir mes rainures ce soir avec la fraise de 10mm !! Quelle tête en l'air !
Prochaine étape donc ce soir: élargissement des rainures, découpe des ailettes, et s'il reste du temps, du "contre-disque" qui viendra par dessus tout çà !
Il faisait déjà -3° dehors, l'atelier n'est pas isolé, il devait pas faire beaucoup plus chaud dedans !
J'ai donc démonté mon ancien "aspirateur".
En fait, la turbine était encore en bon état. Je l'ai fait tourner, elle tourne par contre comme une patate !!
Hors de question de garder ça, je vais donc en faire une nouvelle.
Pour mon prochain test, j'ai donc prévu de la faire en PVC.
J'ai une grande plaque, d'environ 1m par 2m, en 10mm d'épais, cela ressemble plutot à du FOREX: l'âme n'est pas "lisse" comme la surface, mais granuleuse (fin quand meme). Elle semble cependant assez dure, et ne s'enfonce pas sous l'ongle... Ca n'est donc pas une "mousse molle".
Le temps, ou plutot l'experimentation, dira si ca convient... Je me suis un peu documenté sur ce matériaux, il s'assemble comme du PVC classique: usinage aux outils à bois à basse vitesse, collage à la colle PVC, "soudage" (que je ne tenterai pas...)
Allons y, alors, avec la découpe du disque de base de la turbine.
Après avoir coupé grossièrement un carré d'environ 50cm de côté à la scie sauteuse, je traçe ma turbine sur le PVC.
Tout au compas : Je marque le centre, puis un premier diamètre, et le cercle.
J'ai décidé de mettre 8 ailettes à la turbine. Il faut donc diviser ce cercle en 8. En 6, c'aurait été facile, il suffit de tracer une rosace

En 8, ca n'est pas beaucoup plus compliqué, il suffit de se souvenir de ses cours de trigo ! Est ce que mon prof de maths aurait cru qu'un jour j'allais fabriquer une turbine dans mon atelier !
Après avoir tracé le cercle et un diamètre, on fait donc une perpendiculaire à ce diamètre passant en sous centre. Au compas, c'est rapide et précis.
Puis, on trace les 4 bissectrices des 4 quadrants représentés par ces deux droites. Encore facile et rapide au compas !
Voila, mon cercle est divisé en 8, il faut ensuite tracer la position des 8 ailettes.
J'ai choisi de les orienter vers l'arrière (il semble que la turbine garde des performances plus "linéaires" avec cette configuration).
Je trace donc un second cercle , assez petit, au centre du premier, et je décale le tracé de chaque ailette.
Au final, après quelques minutes, on est prêt à défoncer tout ça :
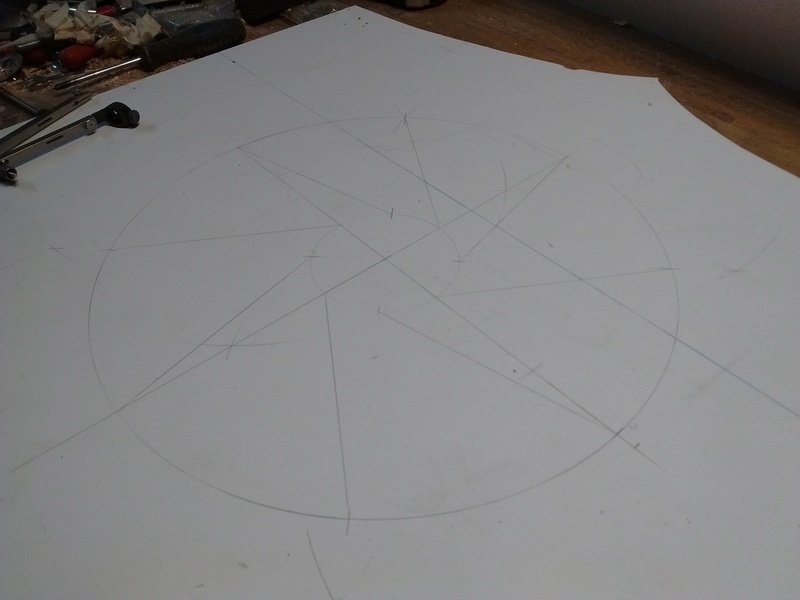
Un petit trou diamètre 5mm au centre, et la défonçeuse prend place avec son compas :
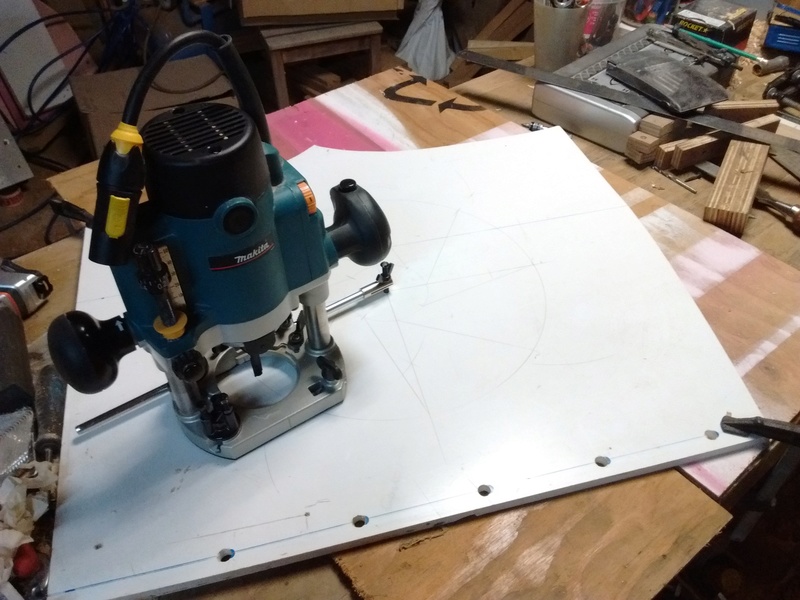
Première passe légère, réglage au plus lent : le matériau se comporte agréablement: Ça fait de petits copeaux, qui ne collent pas.
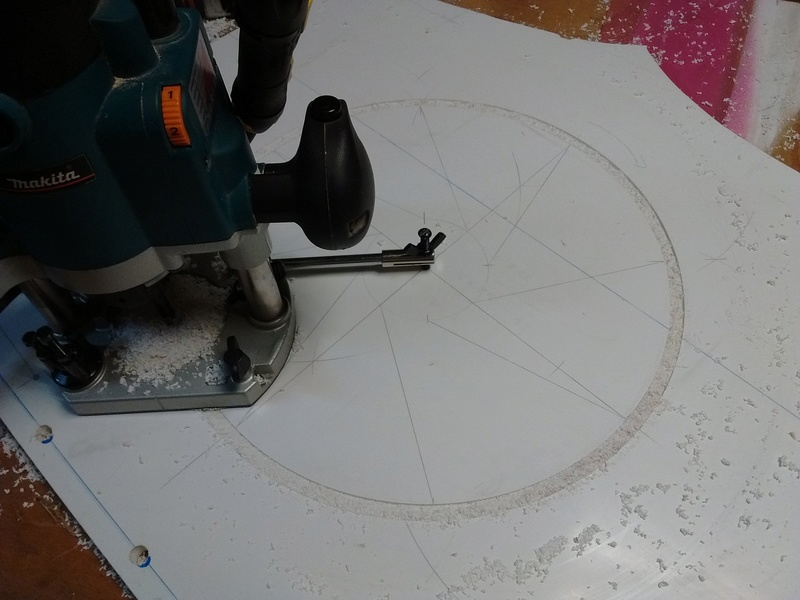
Et voila, le disque est découpé.
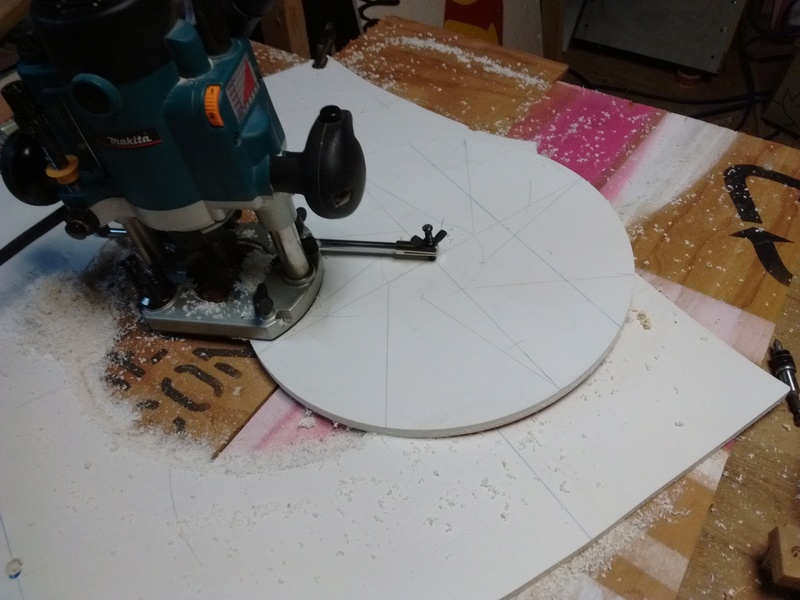
Enfin, je trace une parralèle à 5cm (largeur entre l'axe de la fraise et le coté de la semelle de la défonceuse) de chaque future ailette et je défonce celles-ci.
C'est assez rapide, j'aurais pu me fabriquer un guide, mais il n'y en a que 8 à faire, ca se fait rapidement !

J'ai oublié de prendre une photo une fois terminé ! Oups !
L'établi est tout blanc... J'aurais pu chanter à tue-tête "Il a neigé dans l'atelier..." sur un air bien connu

Enfin, après avoir terminé ces coupes, je me rend compte que j'avais monté une fraise de 8mm sur la défonceuse, et les ailettes feront...10mm d'épais !
Je vais donc pouvoir élargir mes rainures ce soir avec la fraise de 10mm !! Quelle tête en l'air !
Prochaine étape donc ce soir: élargissement des rainures, découpe des ailettes, et s'il reste du temps, du "contre-disque" qui viendra par dessus tout çà !
Re: Encore une nouvelle turbine d'aspi
salut a tous
si ce n'est pas trop tard, je ne peut que te conseiller de faire ta turbine bien plus haute que 5 6cm, ton moteur peut prendre beaucoup plus
pour info, j'en fais tourner une d'environ 32 de diametre par 10 cm de haut avec un moteur de 800 watts, qui consomme a peu pres 650 avec toutes les pertes de charge, notament le separateur thien et le filtre
wandel fait tourner une turbine simmilaire a la tienne avec 1/2 ou1/3 de ch, d'ailleur il y a une video ou le moteur n 'arrive pas a demarrer sans ces pertes de charges' tout ouvert quoi), il est vraiment a la limite
le separateur mange quand meme pas mal de debit, il faut le savoir, et avec 5.5 m de tuyau souple en 100mm( c'est pas idéal je sais), avec un filre encrassé, c'est juste pour la rabot dégau.
si ce n'est pas trop tard, je ne peut que te conseiller de faire ta turbine bien plus haute que 5 6cm, ton moteur peut prendre beaucoup plus
pour info, j'en fais tourner une d'environ 32 de diametre par 10 cm de haut avec un moteur de 800 watts, qui consomme a peu pres 650 avec toutes les pertes de charge, notament le separateur thien et le filtre
wandel fait tourner une turbine simmilaire a la tienne avec 1/2 ou1/3 de ch, d'ailleur il y a une video ou le moteur n 'arrive pas a demarrer sans ces pertes de charges' tout ouvert quoi), il est vraiment a la limite
le separateur mange quand meme pas mal de debit, il faut le savoir, et avec 5.5 m de tuyau souple en 100mm( c'est pas idéal je sais), avec un filre encrassé, c'est juste pour la rabot dégau.
xmax- je prends du galon
- Messages : 95
Points : 181
Date d'inscription : 30/01/2014
Age : 54
Page 2 sur 2 • 1, 2

» Fraisage turbine
» Dépose moteur aspirateur Solo 8 Lurem
» Un petit voyant de débit pour ma 4060
» Fixation ventilo et turbine sur une axe de moteur
» Expériences autour d'un aspirateur Kity 692
» Dépose moteur aspirateur Solo 8 Lurem
» Un petit voyant de débit pour ma 4060
» Fixation ventilo et turbine sur une axe de moteur
» Expériences autour d'un aspirateur Kity 692
Page 2 sur 2
Permission de ce forum:
Vous ne pouvez pas répondre aux sujets dans ce forum